Pipework
The areas most susceptible to
creep damage in high pressure pipework systems are, as in headers, the welds. However, whereas in headers the stresses
are generally determined by the pressure and thermal stresses alone, which are known or
can be calculated, pipe work systems are also subject to highly variable and largely
unquantified external forces. This means that life management procedures for welds have
remained largely experience based despite a great deal of effort expended in trying to
devise quantitative prediction procedures. Qualitative assessment of the severity of creep
cavitation through examination of surface replicas is frequently used for pipe weld life
management.
Metserve Technicians on site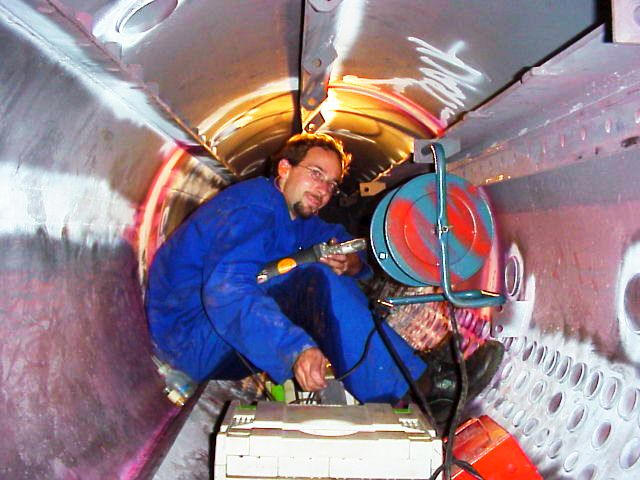
For operation beyond design life
the condition of the parent material also has to be determined. Obtaining material for this is not a
problem but the huge number of heats and individual forgings and castings in a typical
system presents difficulties. Attention may then be concentrated on
critical components
within the system such as T-pieces and, in particular, bends. The latter are more highly
stressed than straight pipes because of thinning and ovality produced during the bending
process as well as the greater potential for stresses generated by system forces.
Experience has confirmed the analytical prediction that outer surfaces are the most
susceptible to creep damage. Methods which have been examined for quantification of
the damage include the usual metallographic surface replication techniques as well
as ultrasonic, magnetic based techniques.
|