Creep
Assessment
Surface replication
and microstructural studies are extensively used to detect creep cavitation and
carbide morphology in service components These techniques are capable of
providing early warning of creep exhaustion in high temperature components, well
in advance of that achievable by conventional NDE methods.
Quantification of
damage e.g. creep cavitation (Cane & Shammas, 1984, and Eggeler, 1991) and
carbide morphology (Masuyama, 1993), has led to the increased confidence in the
prediction of life fraction by these methods.
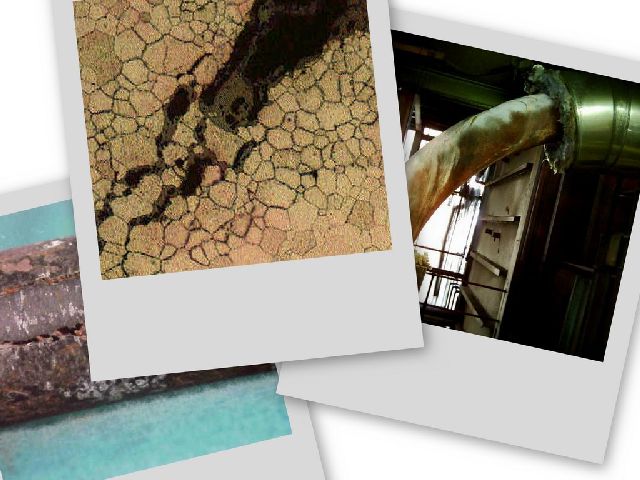
In boiler
headers and
steam pipes, creep is a major cause of cracking, with damage most likely to
appear in localised brittle regions, such as those near welds.
Usually, the first sign of creep damage is the formation of microscopic cavities
at grain boundaries of the heat-affected zone near a weld, which eventually
coalesce and expand into cracks.
The evolution of such creep cavitation can be used to provide an estimate of
service life already expended and of the actions required to prevent failure.
Metserve field team has been involved with creep evaluation at many power station
locally and abroad.
|