Steps for failure
analysis
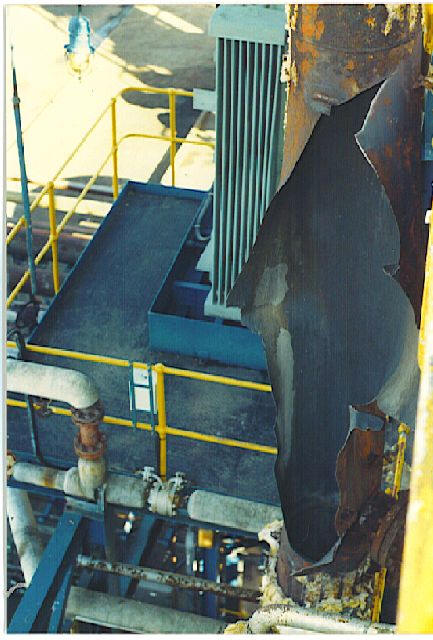
To interpret a failure
accurately, the analyst has to gather all pertinent facts and
then decide what caused them. To be consistent, the analyst
should develop and follow a logic path that ensures a critical
feature will not be over looked. The following steps should be
taken:
Decide what to do. How detailed an analysis is necessary? Before
starting, try to decide how important the analysis is. If the
failure is relatively insignificant, in cost and inconvenience,
it deserves a cursory analysis; the more detailed steps can be
ignored. But this strategy increases the chance of error. Some
failures deserve a 20-minute analysis with an 80 percent
probability of being correct, but critical failures require true
root cause failure analysis (RCFA), in which no questions are
left unanswered. RCFA may require hundreds of man-hours, but it
guarantees an accurate answer.
Find out what happened. The most important step in solving a
plant failure is to seek answers soon after it happened and talk
to the people involved. Ask for their opinions, because they
know the everyday occurrences at their worksite and their
machinery better than anyone. Ask questions and try to get first
person comments. Do not leave until you have a good
understanding of exactly what happened and the sequence of
events leading up to it.
Make a preliminary
investigation. At the site,
examine the broken parts, looking for clues. Do not clean them
yet because cleaning could wash away vital information. Document
the conditions accurately and take photographs from a variety of
angles of both the failed parts and the surroundings.
Gather
background data. What are the
original design and the current operating conditions? While
still at the site, determine the operating conditions; time,
temperatures, amperage, voltage, load, humidity, pressure,
lubricants, materials, operating procedures, shifts, corrosives,
vibration, etc. Compare the difference between actual operating
conditions and design conditions. Look at everything that could
have an effect on machine operation.
Determine what failed. After you leave the site and the
immediate crush of the failure, look at the initial evidence and
decide what failed first—the primary failure—and what secondary
failures resulted from it. Sometimes these decisions are very
difficult because of the size of analysis that is necessary.
Find out what changed. Compare current operating conditions with
those in the past. Has surrounding equipment been altered or
revised?
Examine and analyze the primary failure. Clean the component and
look at it under low-power magnification, 5x to 50x. What does
the failure face look like? From
the failure face, determine the forces that were acting on the
part. Were conditions consistent with the design? With actual
operation? Are there other cracks or suspicious signs in the
area of the failure? Important surfaces should be photographed
and preserved for reference.
Characterize the failed piece and the support material. Perform
hardness test, dye penetrant and ultrasonic examination,
lubricant analysis, alloy analysis, etc. Examine the failed part
and the components around it to understand what they are. Check
to see if the results agree with design conditions.
Conduct detailed
chemical and metallurgical analyses. Sophisticated
chemical and metallurgical techniques may
reveal clues to material weaknesses for minute quantities of
chemical that may cause unusual fractures.
Determine the failure type and the forces that caused it. Review
all the steps listed. Leaving any questions unasked or
unanswered reduces the accuracy of the analysis.
Determine the root causes.
Always ask, "Why did the failure happen in the first place?"
this question usually leads to human factors and management
systems. Typical root causes like "The shaft failed because of
an engineering error" or "The shaft failed because it was not
aligned properly" expose areas where huge advances can be
realized. However, these problems have to be dealt with
differently; people will have to recognize personal errors and
to change the way they think and act.
Laboratory Equipment |